Technology improves quality and feasibility of supported employment
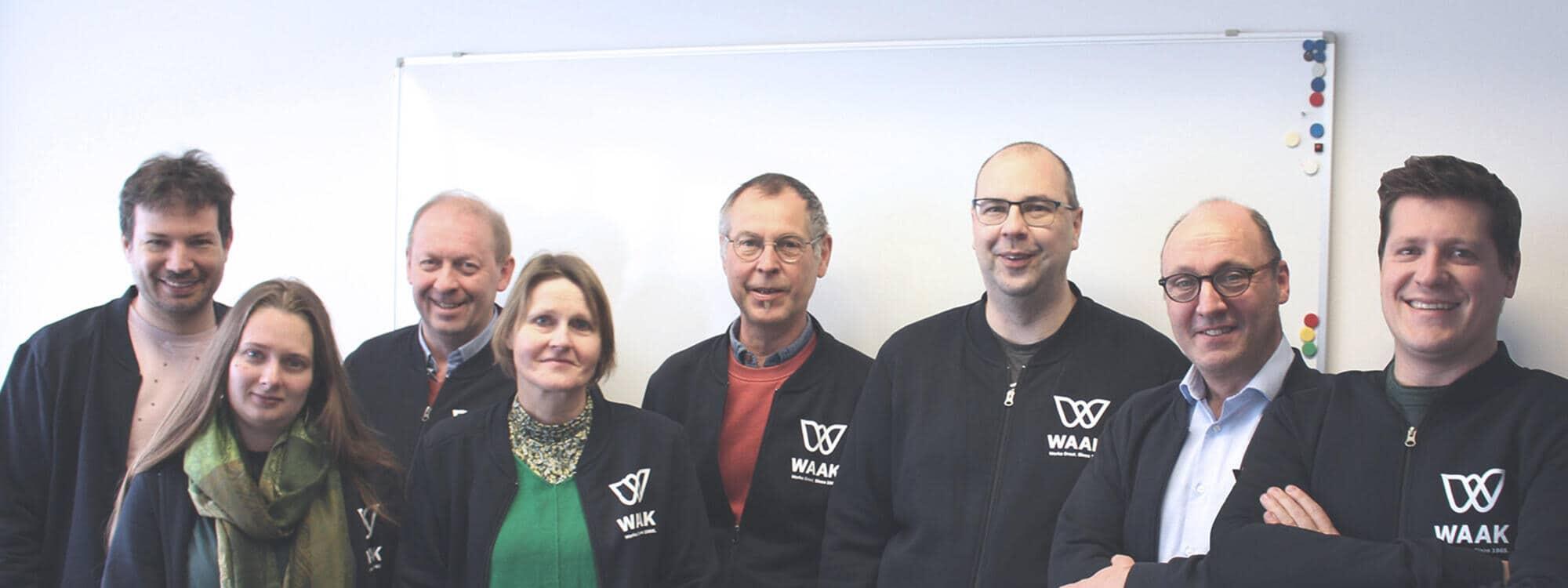
Technology is one of the cornerstones of our company strategy. To us technology is crucial to implement our mission and vision. We use it to bridge the gap between the complex needs of the market and the opportunities and limitations of our staff. At WAAK we have a dedicated team, the Centre of Expertise, that studies how we can use technology, digitisation and automation to further improve our work processes in terms of efficiency, quality and feasibility.
WAAK's Centre of Expertise works on different approaches
The WAAK Centre of Expertise brings together different types of expertise to build one flexible team. Its objective? To research how work – with the use of technology – can be improved. The team is made up of people from different educational backgrounds ranging from electro-mechanics to ergonomics. Thus problems can be viewed and discussed from different perspectives to broaden the scope of the solutions.
Improving work? Our 5 main technological innovation in a nutshell
We would like to put the spotlight on the 5 main tools which we use to improve the work processes at WAAK:
Visualising work instructions
Over the years, we have noticed how important visualisation is for our supported employees. They find written instructions more difficult to understand, either because they have limited reading skills or because textual information is not always clear or can be interpreted in different ways. The Azumuta software solves this problem for us. The program issues the correct work instructions to the person at just the right time. In addition, the instructions are also displayed step by step, which makes it easier for the supported employee to understand them. This not only makes the work easier and improves quality, but it also ensures that they can work independently, which is more motivating for them and gives them a greater feeling of job satisfaction.
Weighing software
It goes without saying that our customers want to receive the exact number of products which they have ordered. In the past, our regular staff would count and package the orders. However, because there were still errors, we developed a weighing software. By using the weight displayed on the scales, the software knows exactly how many units the pack contains. The weighing software always states how many units are still missing or in excess. Given that the system now does the counting instead of the operator, we no longer experience errors. As a result, we can allow our supported workforce to perform the work, and that is the cherry on the cake.
Camera monitoring systems
Ensuring high product quality is of vital importance. When producing cables or cable looms for the HVAC, heat pump or automotive industry, we naturally apply a ‘zero defect standard’ for safety reasons. To enable us to guarantee this to our customers, we have incorporated numerous checkpoints into our system. This not only involves performing manual checks, but also the use of camera monitoring systems. These are specially fitted workstations equipped with cameras taking high-resolution photos. The system algorithm analyses and inspects the image and, if necessary, it will indicate whether any errors have crept in. With the use of the camera monitoring system, supported employees who require more guidance, can check their work themselves, and this gives them a greater sense of independence.
Our Digital Assistance Table (or DAT) is a special kind of camera control system. It takes things one step further than ‘common’ camera control systems. The DAT is equipped with both a camera and a projector. On the one hand, work instructions for the operator can be projected, and on the other, the system also controls the quality of the operator’s work. If an error occurs, the system ‘blocks’, and the operator cannot proceed until the error is resolved. Only then he/she can continue working. In this way, we can guarantee our customers a flawless result. WAAK is an expert in implementing Poka Yoke solutions. The Digital Assistance Table is a prime example of that. With these solutions, we can also employ workers with fewer capabilities without creating additional quality risks. Changes have also occurred in the digitisation of instructions. Digital working instructions are not new, but the possibilities for programming them have become easier and more efficient. It is no longer required to have specialised technical IT knowledge; anyone can do it now. The work of the programmer can now be done by, for example, a work supervisor.
Cobots
At WAAK we make considerable use of cobots. The term ‘cobots’ stands for ‘collaborative robots’. In contrast to robots, which replace the operator, cobots work in collaboration with them. A cobot must therefore be viewed as a mechanical assistant. We mainly use cobots for supported employees who require more guidance. This tool enables them to perform complex processes. Tightening screws, for example, can be a complex process for some of our supported staff. Cobots will assist them with this. The correctly placed cobot will tighten the screw inserted by the operator.
3D printing prototypes
At WAAK, we use 3D printers primarily to print prototypes of gauges for our products. In order to eliminate the possibility of errors, we use gauges to ensure that our workers work in a correct manner. This improves the quality of the final product.
Instead of immediately making a real gauge and using it in the production environment, we first test it with a 3D printed model. This allows us to see if the gauge will deliver the desired final result and if it works for our workers or if it needs adjustments. This approach is not only cheaper, but it also allows us to create a design in sustainable material that is ‘first time right’.
Moreover, 3D printing allows us to create customised gauges that take into account the limitations of the (machine) operator. In other words, we can make toolings that help compensate for their limitations. Thanks to the 3D printed gauges, we can adapt the work to our workers. Thanks to 3D printing we are not bound by machine limitations. It offers us enhanced design freedom
Everyone benefits from this: it improves the quality of the product of the customer and it improves the work of our workers.
Eye tracking
Clear working instructions are absolutely crucial for our supported employees. For us it is important to find out how they use this information, and whether or not they understand the instructions. The Centre of Expertise checks this by means of eye tracking. By equipping our supported employees with smart glasses, their eye movements can be observed. Thus we can deduce whether the instructions are either easy or too difficult, whether they are stressing the supported employee, whether the individual is fully concentrating or easily distracted, etc. This information enables us to improve our work instructions, e.g. by visualising them to an even greater extent or by dividing them into smaller steps.
In collaboration with UGent and Howest, we launched the ‘Expert Gaze’ project. Its aim was to investigate whether doubt can be detected and measured, and whether eye tracking is a good method for it. For this research, workers were equipped with smart glasses. While assembling electric cables, the smart glasses registered the eye movements and gathered data
UGent then analysed the data. Prior to the research, an expectation of the duration and number of eye movements was determined. The researchers expected that the measured results would fit in to that range. This was mostly the case. However, as soon as doubts or confusion arose, the eyes began to make much more movements than what was expected.
Based on this finding, the researchers concluded that doubt (and the stress that goes with it) can be identified in eye tracking data. They also found that eye tracking using smart glasses is a useful tool for this purpose. Finally, they came to the conclusion that the number of eye movements is a good indicator to determine which instructions are clear to the worker and which are not.
Being able to detect doubt, we can now adjust the work instructions of our workers and make them more understandable. Everyone benefits from this. In the first place our workers, because with clear instructions, they experience less doubt and therefore less stress, which allows them to work in a comfortable manner. It is also beneficial for the work supervisors, as they need to intervene less to help the worker. Finally, it is also positive for the customer, because good instructions lead to fewer errors, thus enabling us to deliver a product of the highest quality.
Technology – and especially recent advances in AI and digitisation – is often perceived to make people superfluous. As an innovative social enterprise, we do not go along with this way of thinking. As we see it, technology does not replace the work, but it does make the work easier which actually creates more employment. As a result, people with more limited skills and who require a greater level of assistance, have more work opportunities. For some of our people it makes the labour market a lot more accessible.